Hygienic electric nozzles
The electric HydroPulse is the ultimate in precision spraying. The nozzle has an integrated electrically actuated valve within the nozzle body. As this is very close to the spray orifice it allows the EHP to be cycled on and off up to 150 times per second. This allows for pulse width modulation meaning the amount of spray being delivered can be varied without changing fluid pressure.
Features
- Uses a 24DC electrical power
- Cycles on and off up to 150 times per second
- All stainless steel with food-grade Viton seals
- Hygienic crevice-free design
- Recirculation port as standard
- Uses standard BJ, BJH or CW spray tips
- Pulse width modulation for controlling dosing
- Up to 17 bar fluid pressure
- 3.8 l/minute max flow rate
Flow rates and sprays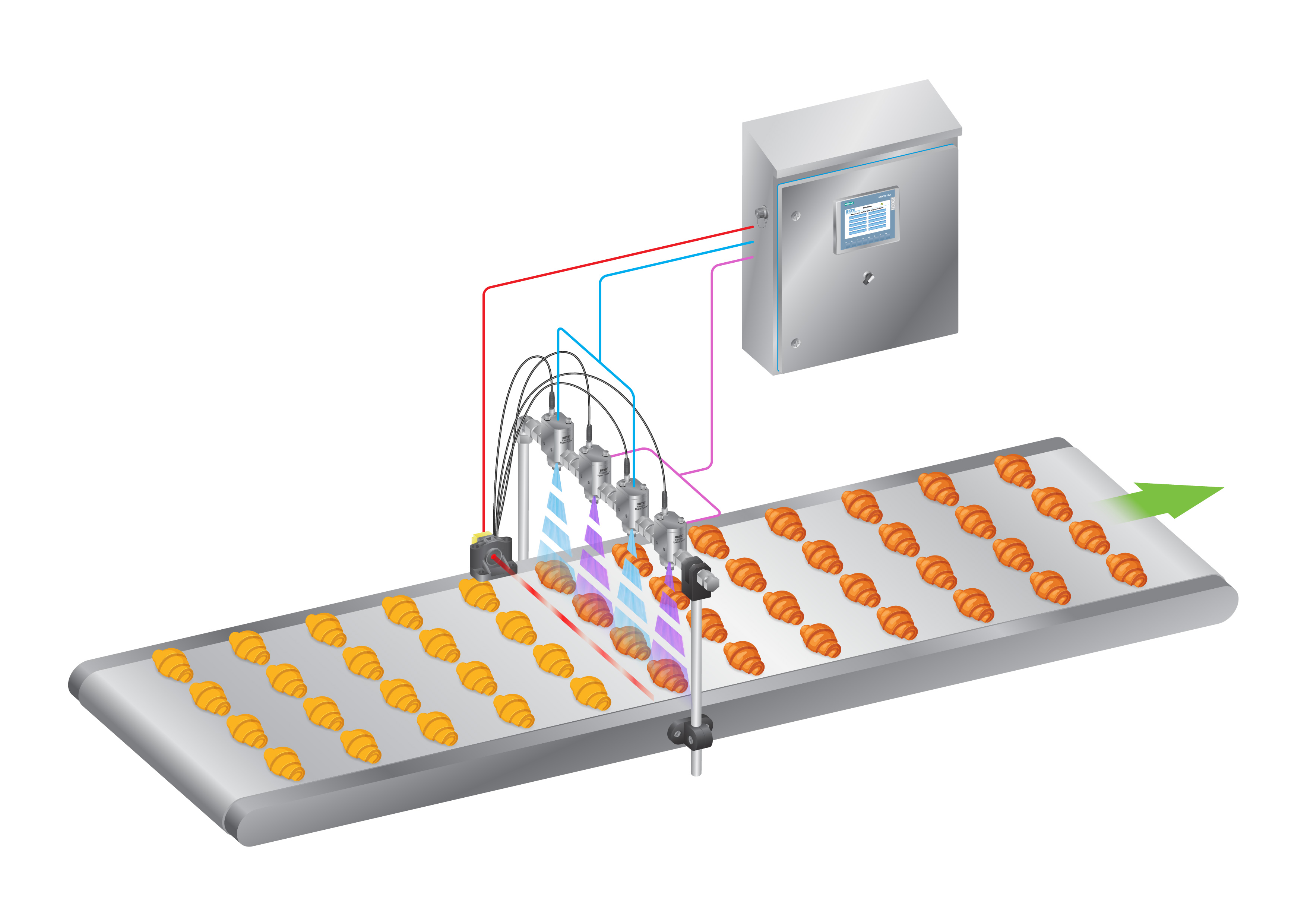
Both flat fan and full cone spray patterns are available from EHP nozzles. Standard flat fan tips and full cone tips can be used. However, the flow rates can be reduced using pulse width modulation allowing for a greater range of flows.
This also allows for the same nozzle tip to be used for different spraying duties, whilst maintaining a constant fluid pressure.
Benefits
When combined with a suitable control system, such as our FlexFlow control panel, the EHP nozzle can deliver variable flow from the same set of nozzles and give highly accurate spraying even on very fast moving production lines. This often means
that wastage or overspraying can be greatly reduced saving money and improving product quality.
General benefits include:
• Control a wide range of flow rates
• Guarantee an even and uniform application rate that connects with conveyor line for automated speed adjustments
• Reduce consumption of expensive coatings
• Reduce overspray waste
and improve product quality
• Exact target coatings secure a clean and safe environment
• Promote increased production
• Reduce maintenance and downtime
• Reliable spray dosing provides an accurate calorie count
Applications in the food industry
There are many applications for EHP nozzles in the food industry. Some common applications include:
• Application of antimicrobial agents for food safety
• Application of preservatives and mould inhibitors to help extend shelf
life
• Application of egg wash
• Coat bottles to minimize scuff damage
• Apply water to balance moisture loss from the freezing process
• Apply coatings and release agents to pans, cookie sheets, and conveyors to prevent
sticking
• Apply flavourings, oil, and butter to enhance the appearance and improve the taste of products
• Apply viscous coatings like syrups, glazes, and chocolate