Industrial electric nozzles
The industrial Electric HydroPulse (EHPi) from BETE is a high-precision spray nozzle. The nozzle has an integrated electrically actuated valve within the nozzle body. As this is very close to the spray orifice it allows the EHPi to be cycled on
and off up to 50 times per second. This allows for pulse width modulation meaning the amount of spray being delivered can be varied without changing fluid pressure.
The EHPi is an industrial variant of the EHP nozzle. This nozzle is designed for non-hygienic spray applications. It can operate at higher pressures than the hygienic variant. This nozzle should be considered whenever high-precision
spraying is required in non-hygienic applications such as in the spraying of engineered wood and other manufacturing processes.
Features
- Uses a 24DC electrical power
- Cycles on and off up to 50 times per second
- Uses standard BJ, BJH or CW spray tips
- Pulse width modulation for controlling dosing
- Up to 20 bar fluid pressure
- 3.8 l/minute max flow rate
Flow rates and sprays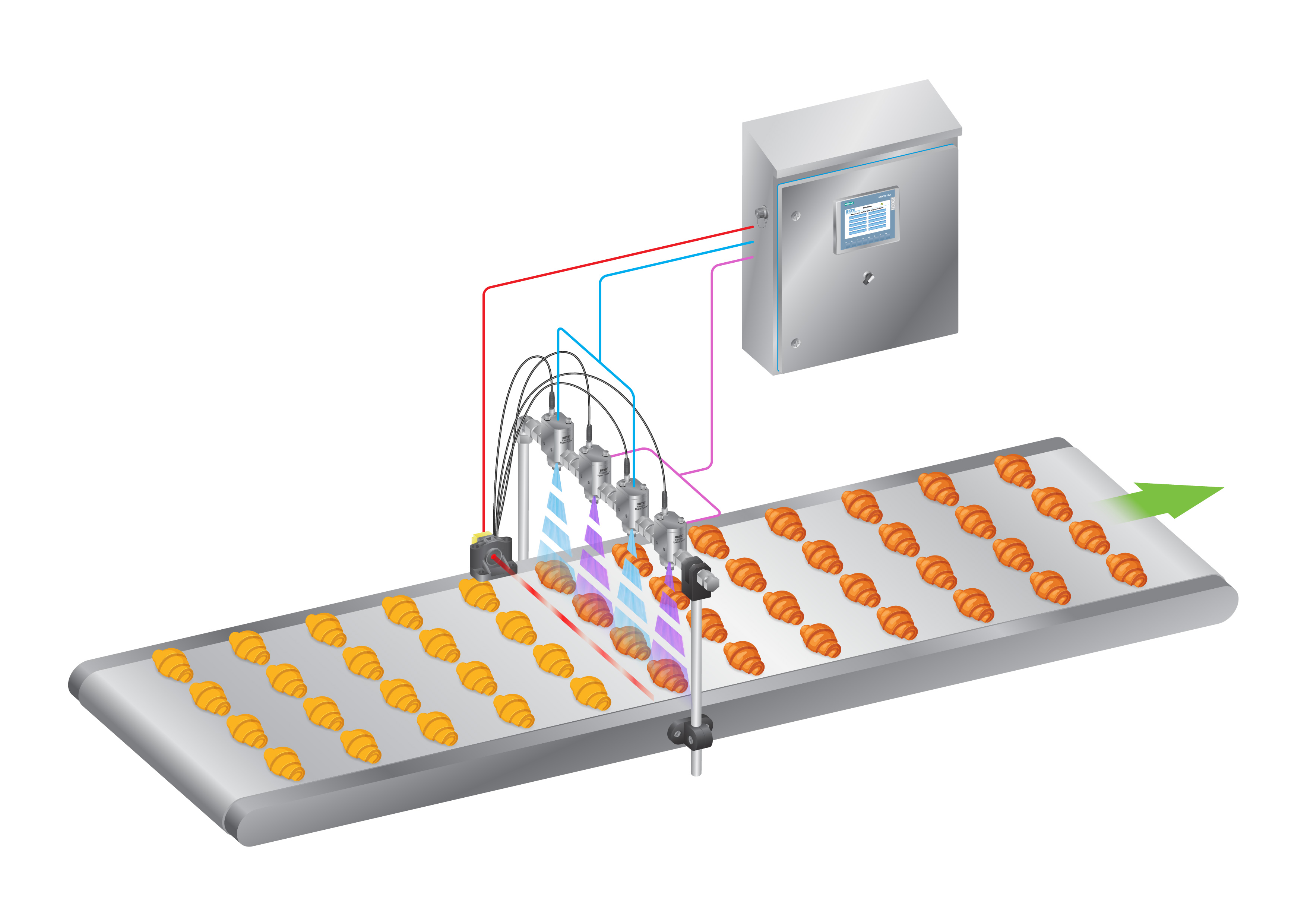
Both flat fan and full cone spray patterns are available from EHP nozzles. Standard flat fan tips and full cone tips can be used. However, the flow rates can be reduced using pulse width modulation allowing for a greater range of flows.
This also allows for the same nozzle tip to be used for different spraying duties, whilst maintaining a constant fluid pressure.
Benefits
When combined with a suitable control system, such as our FlexFlow control panel, the EHP nozzle can deliver variable flow from the same set of nozzles and give highly accurate spraying even on very fast moving production lines. This often means
that wastage or overspraying can be greatly reduced saving money and improving product quality.
General benefits include:
- Ensure precise application and reduce waste
- Integrate tonnage or line speed to maintain uniform coverage when variables change
- Reduce the use of expensive resins, waxes, or release agents by applying the exact volume required
- Apply the optimal amount of surface moisture to increase production by decreasing time in the press
- Confidently transition to running full pMDI products with non-stick press protection
- Eliminate compressed air from most pre-press and wax operations
Industrial applications
Apply pMDI or LPF resin in the blender Apply slack wax, tallow wax or e-wax in the blender Add surface moisture before pressing boards Apply mixed release agent on mats, cauls, or press belts when using pMDI resins Mark nail lines on oriented strand board (OSB)