Tank cleaning for dairy processing
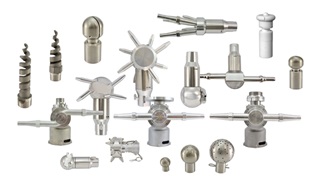
Strict hygiene is of vital importance in all aspects of dairy production. The cost of poor cleaning can be catastrophic resulting in ruined batches, product recalls or worse still contaminated and potentially pathogenic product reaching the market. No dairy producer survives long if they skimp on hygiene standards.
A variety of different vessels are used in dairy
production, be they fermentation tanks for yogurt or cheese making, maturation tanks for ice cream, pasteurizing tanks or milk silos, they all need regular cleaning. For small or open topped tanks manual cleaning has been common practice for decades but for larger and closed tanks permanently installed cleaning heads are now
the norm. These heads will run through a cleaning cycle to ensure the tank is clean. A wide variety of different cleaning heads are available from the SNP from simple spray balls to powerful and efficient rotary jet cleaners.
We work with dairy industry professionals to optimise tank cleaning systems. Often with good cleaning head selection significant water and energy can be saved.
Stages of the cleaning process
Depending on the type of tank and residues the cleaning cycle will run in a number of phases normally including some or all of the following key stages.
1- Pre-rinse. To wet the product residue.
2- Wash. This is designed to remove any residue on the tank wall so that the entire surface area is exposed for the sanitising stages.
3- Alkali caustic. This will break down protein and fat residues making them easier to wash off
4- Acid caustic. An acid stage will be used to break down mineral deposits (milk stone)
5- Final rinse. A clean water rinse to remove any contaminants remaining from previous stages.
The wash stage is critical to get right because a failure to remove the bulk of the residue will mean that the caustics may not get into contact with their targets as they are protected under a layer of grime. This means fats, proteins and minerals may build up over time allowing a place for bacteria to grow.
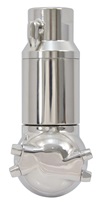
Impact cleaning
Moving to impact cleaning devices is an easy way to save water and improve tank cleaning effectiveness. Static spray balls rely on the cascading of water down the walls of the tank to gradually remove residues. This is effective for easily water-soluble grime but non water-soluble residue and/or sticky residue will not be removed quickly. Heating the water helps break down such fouling but even with heated water it takes time and a lot of water to remove many common residues found in dairy processing tanks. In particular Greek yogurt fermentation tanks are problematic and difficult to clean.
Rotary jet cleaners deliver high impact cleaning jets to the tank wall. These explode outwards blasting off any residue. The main cleaning mechanism is the impact of the jets themselves rather than the cascading of water down the tank's wall, although secondary cleaning occurs as this happens as well. Impact cleaning is far more water efficient meaning that even a tough residue can be removed with minimal water. Jet cleaners will also remove residues in a fraction of the time. This means that the water consumption per cleaning cycle can be reduced considerably.
Further benefits
Because residues are removed more effectively by impact cleaning machines it may also be possible to reduce the heat and chemicals used. This can clearly have some immediate financial benefits as well as environmental. For more details on optimising the cleaning mix please read the technical paper linked by clicking the icon button.
Easy to swap
SNP have developed a new breed of fast cycle jet cleaners that will run on similar pressures and flow rates to existing spray balls. This means that they will be able, in most cases, to be run on the same CIP feed system as the existing cleaning heads. There is no need to change pipework, pumps or tank openings making it easier than ever to swap to the more efficient cleaning heads. Please call us to arrange a trial and see how much water you can save right away!