Wetting in sanitising sprays
Over-wetting can be an issue in many sanitising situations. If the area being treated contains electrical equipment, then over-wetting may cause damage to the said equipment. Alternatively, a damp surface may present a slip hazard or be undesirable for
other reasons. Wet surfaces will dry out eventually, but the speed of evaporation will depend very much on environmental conditions and the level of wetting.
Whilst over-wetting may be problematic, under-wetting will mean a surface has not been treated. The contact time to effectively kill pathogen varies greatly from pathogen to pathogen but the World Health Organisation recommends 10 minutes
of contact time for killing viruses and longer for some hard-to-kill bacteria. This being the case, it is clear that under-wetting that will evaporate before this time will be sub-optimal.
As with many things a balance is required between under and over-wetting. It should be noted that wet does not necessarily mean wet to the touch. A micro-coating of disinfectant may not actually even feel wet or present an electrical hazard. These micro-coatings may well be present long enough for a good pathogen kill rate. So, it would be an error to assume that everything must feel wet to the touch in order to ensure good disinfection.
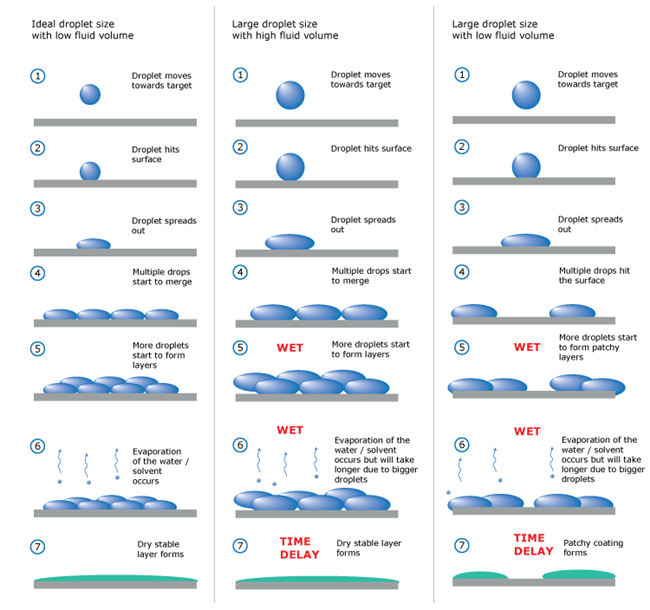
Sprays
For surfaces that can tolerate wetting, but need to dry quickly a fine mist of spray in the 40-100 micron range will be ideal. This will ensure good coverage due to the small droplet size and will give a good contact time. If the level of spraying is
controlled carefully and it is distributed well over an area then drying can occur naturally in a matter of minutes. The surface can be dry to the touch quickly, ensuring slip hazards or other undesirable outcomes of damp surfaces are avoided. If
very fine sprays are not achievable then a secondary action like wiping or assisted air drying may be required to evaporate the larger droplet and/or to help cover patches of the surface that did not come into contact with the spray.
Wet Fogs
Fogs will reduce the wetting problem greatly. Even a wet fog (10-40 microns) can, when used properly, be used safely around electrical equipment and the surfaces being treated may not even feel wet to the touch. Any slight dampening that does occur will
very rapidly evaporate leaving the surface dry. Care needs to be given that the contact time between the surface and the disinfectant is sufficient to ensure good pathogen elimination.
To avoid wetting with wet fogs the nozzle should be positioned far enough from the target to ensure sufficient spray distribution. If the spray volume is spread over a wide area the wet fog will form a microlayer on the target surface that will not feel
wet to the touch. This will give excellent surface coverage and wetting concerns can be eliminated. Again, care needs to be given to ensure that the contact time is sufficient to remove pathogens before evaporation occurs.
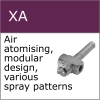
Dry fogs
As the name suggests, dry fogs will not cause wetting. Even when sprayed very close to the target surface it is extremely unlikely to experience any significant wetting. Such fogs are safe to use around sensitive electrical equipment and wetting concerns
are eliminated. The downside of this is that contact time between the fog and surface-dwelling pathogens may be minimal. This is especially true if the pathogens are shielded from direct contact with the air by grease or grime. If a surface is wet
then the disinfectant may penetrate small layers of shielding dirt or grime but this is unlikely to happen with dry fogs precisely because they are dry.
Dry fogs are extremely effective at removing airborne pathogens. They are also extremely mobile meaning they will naturally fill any air space they are deployed in. As such they are a very useful tool in disinfecting systems but should not be considered
as a magic bullet due to their potential downsides when tackling surface-dwelling pathogens.
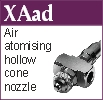