Eductor nozzles
Eductor nozzles are positioned under the surface of fluid in a tank in order to keep it in motion. The liquid in the tank is circulated through the eductors so that it is 'turned' over a period of time to ensure that sedimentation or liquid separation does not occur. Eductors have gaps at the back of the nozzle casing that allow surrounding fluid to be drawn in and moved in addition to fluid being pumped through the nozzle. This means that about 5 times the pumped fluid is actually moved by an educator.
Sizing eductor nozzles
Like all nozzles eductors have a flow rate that is proportional to the pressure drop across the nozzle. So it is a simple matter to consult the flow rate vs pressure charts for eductor nozzles to determine how quickly they will 'turn' the fluid in the tank. One 'turn' is defined as moving the whole volume of fluid contained within the tank. So, given that eductors move 5 times their motive flow rate, eductors should be sized to 'turn' 1/5th of the fluid in the appropriate time.
The 'turn' time will vary greatly depending on the application but typically ;
A general circulation of fluid with no solids only 1-3 'turns' per hour will be required.
For mixing fluids to keep solids suspended between 5-10 'turns' per hour are required.
For plating and rinsing tanks between 10-25 'turns' per hour are required.
For blending applications anything between 20-120 'turns' per hour
These are general rules of thumb and some variations outside these guides may occur from specific applications.
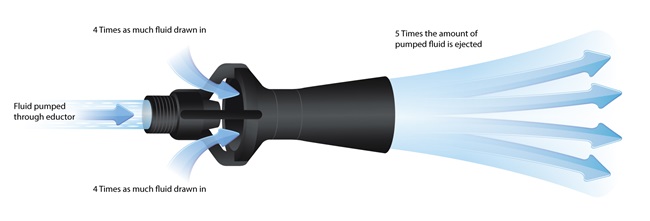
Positioning of eductor nozzles
Eductors will produce a plume of moving fluid. These will tend to have a length equal to 4.3 metres per 1 bar of pressure drop across the eductor. The plume will have a 'spray angle' of around 12 degrees and so forms a narrow cone of moving fluid. Ideally edcutors should be positioned so that these plumes hit the opposite wall of the tank and so further dissipate as they do so.
Little mixing will occur below the eductors so they should be positioned low in the tank and angled upwards. But if no sedimentation is to be tolerated then a set of eductors can be angled downwards to sweep along the floor of the tank. In such cases the 4.3m/1 bar plume reach should be halved to 2.15m/ bar.
Ideally one should aim to cover as much of the tank as possible with the estimated moving plumes. In this way an even mixing/agitation will occur with no 'blind' spots that will allow for sedimentation to occur in parts of the tank. This will normally necessitate multiple eductors per tank.
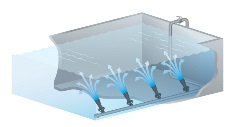
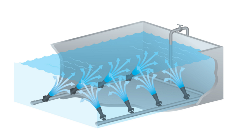
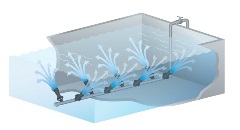
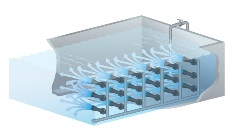
Adjustable holders
It is very common to attach eductors to pipework with adjustable nozzle holders that allow for the eductor to be moved 45 degrees in two dimensions. This means that the final plume directions can be adjusted in the field for optimum coverage.
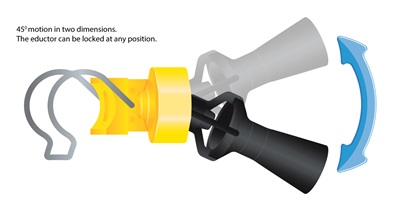
Eductor models
We offer two ranges of eductors. For metal nozzles the TurboMix eductors from BETE are made as standard in 316 stainless, cast iron or brass but in principle can be made in any metal desired. The Uni Eductor from Uni-Spray is made in either glass filled polypropylene or PVDF (Kynar) and form part of the Quik Fit system for pre-treatment spray tunnels. Datasheets on both ranges can be accessed by clicking on the boxes below.
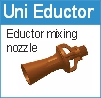
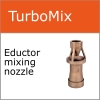