Gas cooling for the chemical industry
The quenching of hot gases is vital in many chemical production processes. This can be to slow gas flows to improve scrubber efficiency or to protect infrastructure further down the process line. There are two basic types of spray cooling system: dry,
where complete evaporation is required; or wet, when only partial fluid evaporation is achieved. In both types droplet size plays a critical role as this determines the overall surface area presented to the gas and hence the overall rate of heat exchange.
Variable load gas quench
Variable loads in cooling systems necessitate specialist nozzles such as air atomising or spillback types which allow flow rates to be adjusted whilst maintaining a steady droplet size. With standard hydraulic nozzles the only method of controlling flow rate is by changing the pressure seen by the nozzle. A certain degree of variable flow can be achieved in this way, how much will depend on the pressure/flow capacity of the pump feeding the system The issue with varying flow by fluid pressure is that the droplet size will also change, getting smaller at higher pressures and bigger with lower pressures. Changes in drop size will change evaporation rates in the quench system.
With air atomising nozzles the presence of compressed air gives another variable with which to change spray properties. A far greater variance of flow can be achieved from a single nozzle. In addition, control over droplet size can be achieved by varying the fluid/air mix.
Another solution to the variable flow issue is the spillback nozzle. This design of nozzle takes some of the fluid flow and recirculates it within the nozzle. The amount of fluid that is 'spilled back' can be varied which allows for the fluid ejected from the nozzle to be varied by a factor of 10 or more. Due to the nozzle being subjected to the same pressure regardless of the flow a fairly tight band spectrum of droplet sizes can be achieved.
Quench system deployment
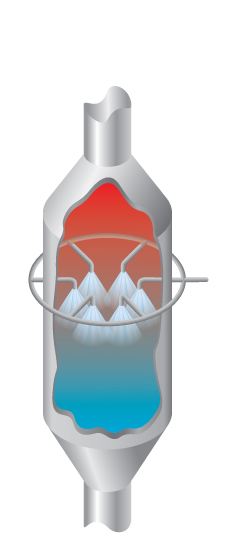
There are many different designs of gas quench system. Positioning the nozzles for optimal coverage is important in all. This will require anything from a simple spray lance to the fabrication of complex nozzle manifolds.
SNP can help with the design and fabrication of all such nozzle positioning infrastructure. We work in a wide variety of materials including high-grade stainless steels and high-temperature alloys such as tantalum.
Spray nozzle selection
• Smaller droplets to aid in speedy evaporation
• Larger droplets to penetrate fast gas flows
• Temperature resistant materials for very hot gas flows
• Variable flow nozzles to cope with variable gas loads
Spiral nozzles will give smaller droplet sizes than other equivalent flow rate nozzles and have a wide available range of spray angles. This makes them ideal for many quench applications.
MP nozzles will give larger droplet sizes whilst this reduces the surface area of the spray. This can be useful in fast gas flows to avoid entrainment and mist eliminator overload.
The Spiral Air (SA) is a high flow rate air atomising nozzle suitable for many gas cooling applications where air is available.
Our spillback nozzles allow for great variation in flow rates whilst keeping droplet sizes stable making them ideal for variable load gas cooling systems.